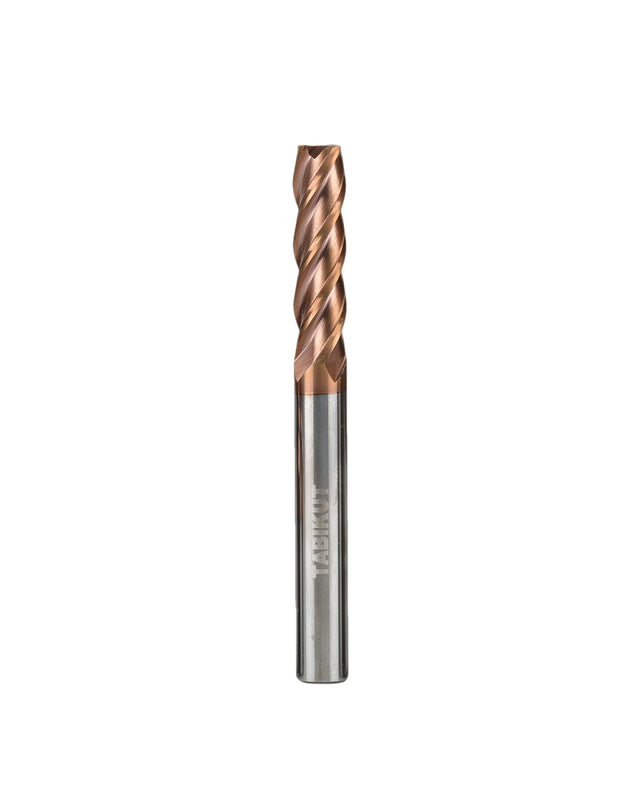
End Mill Cutter: Everything You Need to Know
When it comes to metalworking and CNC tools, precision and efficiency are the two most important factors. If you're cutting, profiling, or slotting, the right tool can make the difference, and among the most important tools to use is the end mill cutter.
If you're trying to learn the purpose of an end mill cutter, how it functions, the various types of cutters available, and how to pick the best one, this comprehensive guide will help you.
What is an end mill cutter?
An end mill cutter is a cutting tool that is used for milling purposes. In contrast to a drill bit, which cuts in a straight line, an end mill can cut in a variety of directions - side-to-side, downwards, and, in some instances, upwards. It is typically used for vertical milling machines as well as CNC machine tools
End mills come in a variety of sizes, shapes, and materials, each specifically designed to perform a specific task and materials.
Basic Parts of an End Mill
Before we get into the details, we'll examine the most important elements of a cutter for the end:
- Shank: The smooth part that is fixed into the collet or holder.
- Flutes: The cutting edges that cut through material. More flutes equal a smoother finish but less chip clearance.
- Cutting Diameter The dimension of the cutting area of the tool.
- Helix Angle: The angle of the flutes that influences cutting and chip removal force.
- End Style: Can be flat (square end), ball nose, or corner radius based on the purpose.
Types of End Mill Cutters
End mills are classified by shape, purpose, and design of the flute. These are the most popular types:
1. Square End Mill
- Blades of flat cutting.
- Ideal for milling shoulders, slots, and flat surfaces.
- Also called flat-end mills.
2. Ball Nose End Mill
- Rounded tip.
- Great for 3D contouring as well as curves on surfaces. Perfect for 3D contouring and curves.
- Common in mold and die work.
3. Corner Radius End Mill
- Has a slight radius in the corners.
- More durable than the square ends and helps prevent chipping.
4. Roughing End Mill
- Serrated flutes that can remove massive materials quickly.
- Produces a rough finish but increases productivity.
5. Finishing End Mill
- The design was created to allow for light passes to create seamless surface finishes.
6. Tapered End Mill
- Tapered cutting diameter.
- It is used in mold and die manufacturing for deep cavities as well as wall angles.
7. Double-End Mill
- Cutting edges at both ends.
- Economical option if wear is evenly dispersed.
Materials Used in End Mill Cutters
The material used to make the cutter is an important factor in the life and performance of the tool.
High-Speed Steel (HSS)
- Cost-effective and flexible.
- Perfect for general-purpose milling on soft materials.
Cobalt Steel
- Better resistance to heat than HSS.
- Suitable for harder metals like stainless steel.
Carbide
- Extremely durable and wear-resistant.
- Ideal for applications that require high-speed CNC machining and hard materials.
Coated End Mills
- Coatings such as TiAlN, AlTiN, and TiCN improve the performance as well as the heat resistance and the life of tools.
Flute Count and Geometry
The design and number of flutes impact chip removal as well as surface finish
- 2 Flutes: More space for chip elimination; great for softer materials such as aluminum.
- 3 Flutes A balance between chip clearance and finish.
- 4+ Flutes Softer surfaces and stronger tool cores. They are used in more brittle materials.
Helix angle is also important:
- Low Helix ( deg) A stronger edge for roughing and harder materials.
- High Helix (40°+): Better removal of chips, ideal for plastics and aluminum.
Common Applications of End Mill Cutters
End mills are utilized in a range of machining jobs:
- Slotting: Cutting narrow slots or grooves.
- Profiling: Creating 2D and 3D part contours.
- Pocketing: Removing large sections of material from the boundary.
- Faceting: Making flat surfaces on the workpiece.
- Engraving Utilizing small-diameter instruments for marking or cutting intricately.
- Drilling Certain end mills have a center cutting feature and can be used as a drill.
How to Choose the Right End Mill Cutter
When deciding on the end mill to use, you should consider the following factors:
Factor | Consideration |
Material | What do you intend to cutsteel, aluminum, or plastic? Use coated carbide for the hardest metals. |
Tool Material | Select HSS to use for all-purpose work, while using carbide for high-speed precision work. |
Flute Count | Fewer chip clearance and roughing; greater for the finishing. |
Cutting Diameter | Find the right size of the part you're making. |
Coating | Make use of TiAlN as well as AlTiN for high-temperature and hard processes. |
Machine Capability | Think about spindle speed, type of holder, and machine rigidity. |
End Mill vs Drill Bit: Key Differences
Feature | End Mill Cutter | Drill Bit |
Cutting Direction | Radial and Axial | Axial-only (straight down) |
Geometry | Flutes flow along the sides and the tip | Pointed tip without cutting sides. |
Applications | Milling, profiling, slotting, etc. | Drilling holes |
Tool Versatility | Highly adaptable | Specific to hole-making |
Best Practices for Using End Mill Cutters
- Use Correct Speeds and Feeds
- Follow the manufacturer's instructions to avoid breakage or wear on the tool.
- Utilize precision collets, shrink-fit or hydraulic holders, to minimize runout.
- Dull cutters can harm components, causing a poor finish.
- Reduce the length that the tool extends out from the holder to decrease vibration.
- Make use of the high-efficiency milling (HEM) or adaptive toolpaths for faster removal of material.
Maintenance Tips for Longer Tool Life
- Clean after use to prevent chip build-up.
- Keep them in dry, well-organized tool holders for your tools.
- Use coolant or air blast to remove chips from milling.
- Examine flutes on a regular basis for dull edges or cracks.
Top Brands Offering Quality End Mills
Some internationally recognized brands include
- Kennametal
- Sandvik Coromant
- YG-1
- OSG
- Dormer Pramet
- Niagara Cutter
These brands are renowned for their consistency in quality, innovation, performance, and consistency.
Conclusion
The end mill cutter is an essential tool in the metalworking and machining industry. With the correct choice settings, setting and handling end mills, they can boost productivity, increase precision of parts, and prolong the life of the tool. If you're an experienced machine operator or just beginning your journey, knowing the basics of end mills will give you an important advantage in machining.
As technology in machining improves and technology improves, so do the designs for the end mills. Keep testing, learning, and improving to stay ahead of manufacturing with precision.